Einblicke in die Montage des Bugatti Chiron.
Das Tor zum Himmel liegt für Autofans ca. 30 Kilometer südwestlich von Straßbourg im Elsass. Dort hat der Autogott seine Engel stationiert. Damit ihnen nicht langweilig wird, montieren sie für uns Erdlinge das Maß der Dinge: Im 10.000-Einwohner-Ort Molsheim entsteht der Bugatti Chiron. Das über 1.000 Quadratmeter große Atelier (gut, so nennen die das bei Bugatti, man darf auch Tempel sagen) wurde 2005 für die Produktion des Bugatti Veyron übernommen. Nach diversen Umbaumaßnahmen startet hier jetzt die Niederkunft der ersten Chiron.
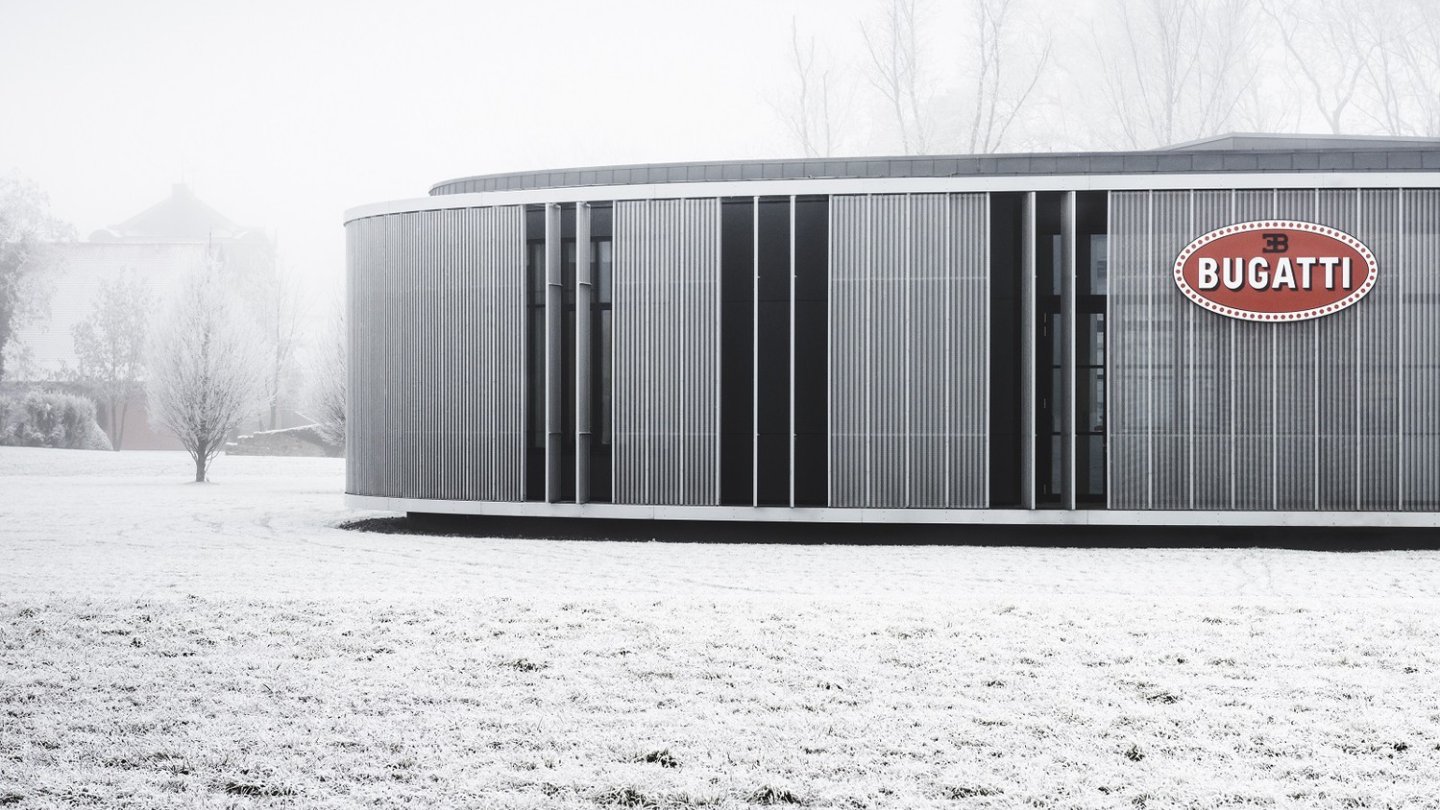
12 Fahrzeuge befinden sich aktuell im Entstehungsprozess, maximal 70 Bugatti werden pro Jahr aus dem Tor zur ersten Abnahmefahrt rollen. Ungefähr zwei Monate dauert es vom Produktionsstart bis zur Fertigstellung eines Chiron. In dieser Zeit montieren 20 Mitarbeiter aus circa 1.800 Einzelteilen das stärkste und schnellste Serienfahrzeug der Welt. Fast die gleiche Anzahl an gut ausgebildeten Menschen, nämlich 15, arbeitet zusätzlich in der Qualitätssicherung. Die hat bei einem Auto, dass nach Kundenwunsch individualisiert schnell mehrere Millionen Euro kostet, natürlich einen großen Stellenwert.
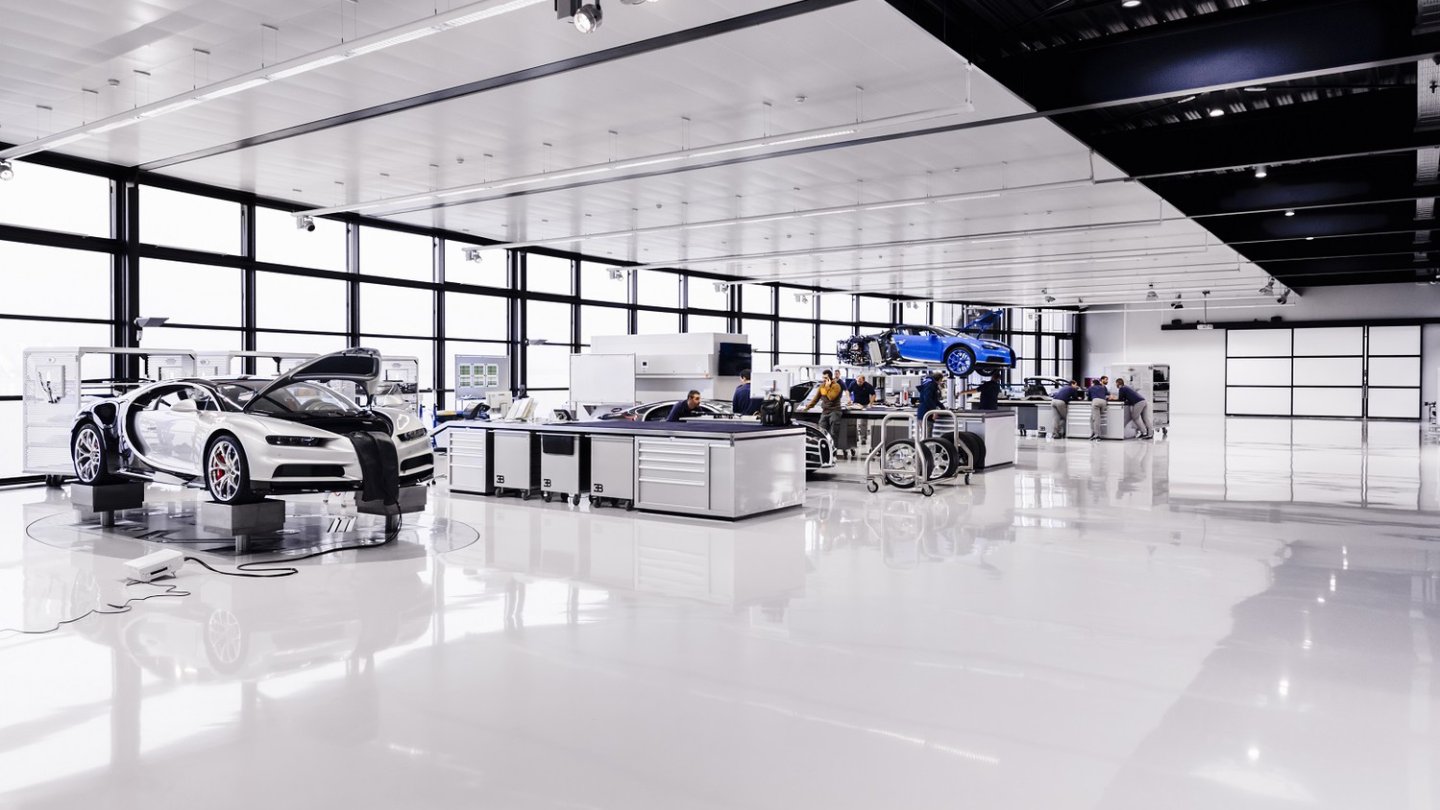
Der Kunde ist häufiger Gast in Molsheim. Er kann sein Auto zusammen mit einem Bugatti-Designer konfigurieren, sich auf Basis von 23 Decklackfarben, acht Sichtkarbon-Varianten, 31 Lederfarben und acht Alcantaratönen das Auto nach seinen Wünschen zusammenstellen. Dazu kommen 18 unterschiedliche Teppichvariationen und alleine elf Farben für die Sicherheitsgurte.
Eine Qual der Wahl bei dieser Auswahl? Kein Grund zur Sorge, man kann sich seinen Bugatti natürlich auch mit der Lederfarbe des Aktenkoffers, in dem die vierte Million damals transportiert wurde und mit dem Lackton von Mutters Fingernägeln kreieren lassen. In der Regel vergehen sieben Monate, bis ein typischer Bugatti-Kunde seinen Chiron fertig konfiguriert hat. Der Gegenentwurf zum Mittagspausen-Geklicke im Web-Baukasten eines profanen Automodells also.
Dann kann Bugatti alle benötigen Einzelteile bestellen. Circa vier Monate später beginnt dann die Arbeit am Kundenauto. Alleine drei Wochen werden benötigt, um die einzelnen Lackschichten nach Bugatti-Maßstäben aufzutragen. Dabei wird jede einzelne von bis zu acht Schichten aufwendig von Hand geschliffen und poliert, bevor eine weitere Lage aufgespritzt wird.
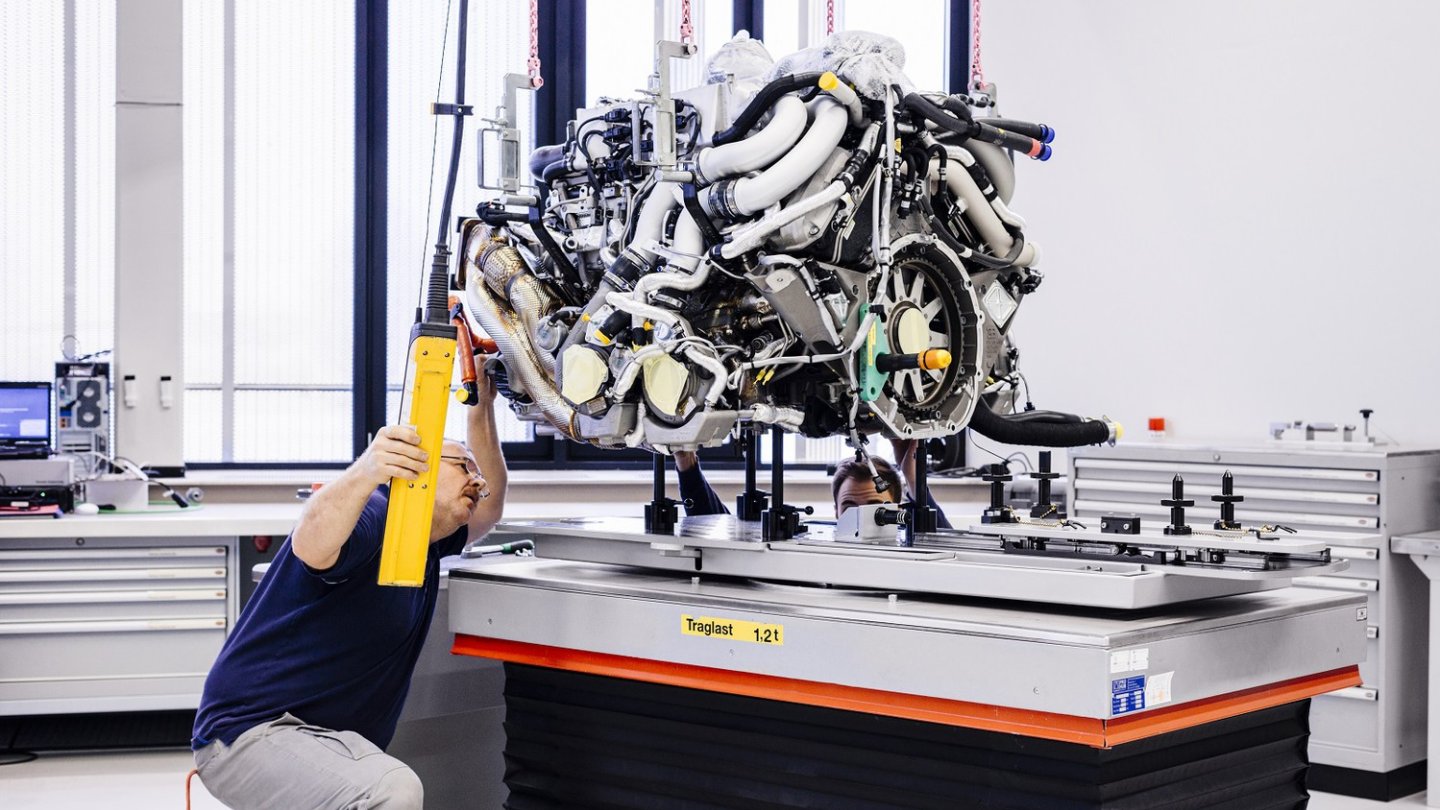
„Wir haben hier in Molsheim eine kleine Manufaktur mit einem kleinen Lager. Sowohl unsere Anlagen als auch die Abläufe können nicht mit anderen Autoproduktionsstätten verglichen werden, erklärt Christophe Piochon. Der 40-jährige Diplom-Ingenieur und Maschinenbauer ist in der Bugatti-Geschäftsführung verantwortlich für die Produktion. So ist der Entstehungsprozess also genauso einzigartig wie das Produkt. Der Boden ist aus glänzend-weißem Epoxid, Bugatti will die Atmosphäre mit dem „Laufsteg eines Modehauses“ verglichen wissen. „Das ist Haute Couture de l´Automobile“, führt Christophe Piochon aus.
Kein einziger Roboter ist im Molsheimer Atelier zu finden. Viele Teile werden vormontiert angeliefert. Der Achtliter-16-Zylinder-Motor mit 1.500 PS brüllt hochdeutsch. Er wird aus Salzgitter bei Braunschweig angeliefert, wo er sich schon acht Stunden auf dem Prüfstand austoben durfte. Auch das 7-Gang-Doppelkupplungsgetriebe wird dort auf Herz und Nieren getestet, bevor es seinen Weg in den Supersportwagen findet.
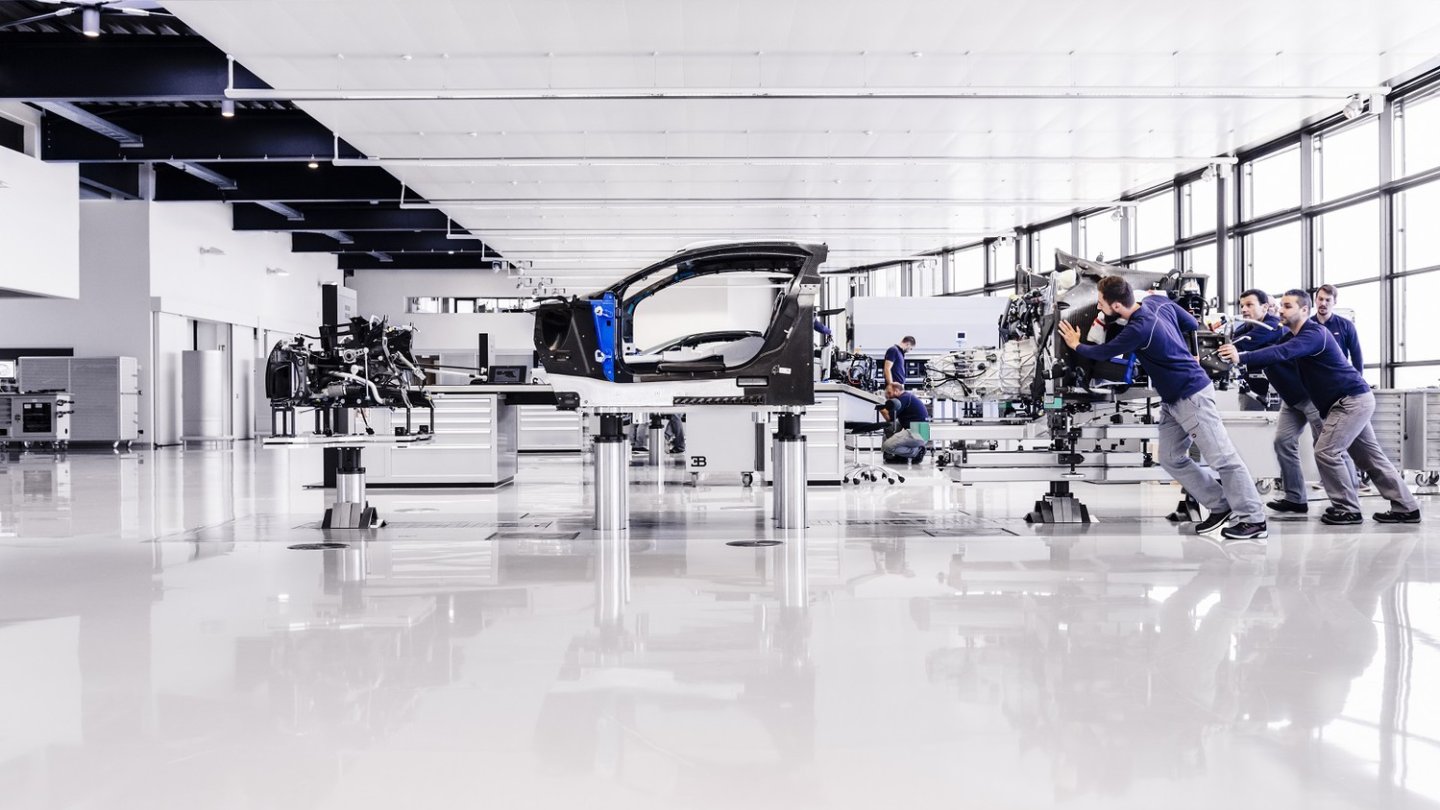
Nachdem das Monocoque und der Hinterwagen samt Antriebsstrang mit 14 Titanschrauben (eine Schraube wiegt nur 34 Gramm) Hochzeit gefeiert haben, kommen erstmals Räder an die Maschine. Anschließend kommen alle Flüssigkeiten, also Motor- und Getriebeöl, Bremsflüssigkeit, Hydrauliköl und Kühlmittel, in den Bugatti. Ein glücklicher Mitarbeiter darf dann den Knopf drücken, der den W16-Motor das erste Mal im Auto anlässt.
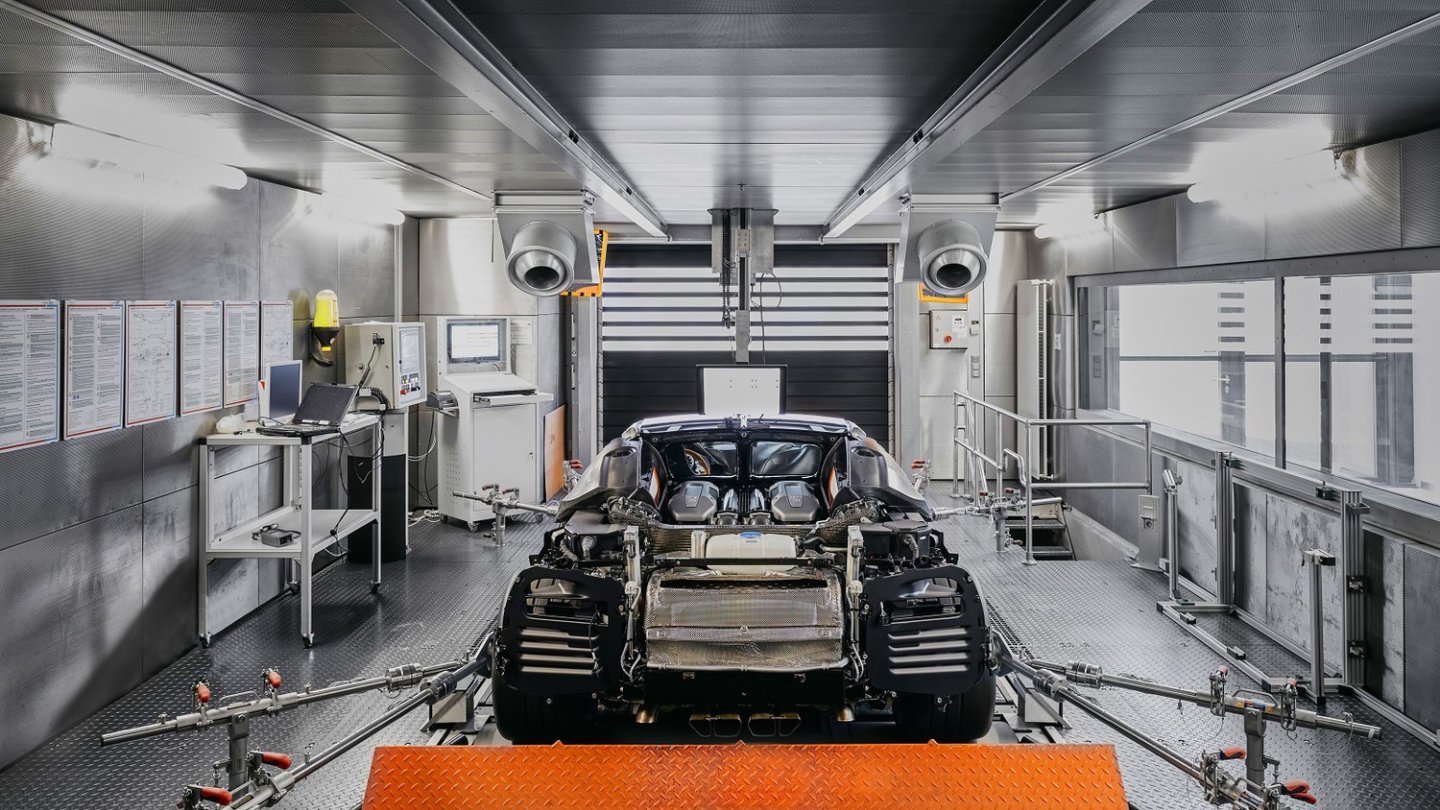
Dann geht es auf den Rollenprüfstand. Von dem profitiert auch die Region, denn während bis zu 1.500 PS und 1.600 Nm Drehmoment auf die Rollen wirken, produziert er elektrische Energie mit einer Stärke von bis zu 1.200 Ampere, die ins örtliche Versorgungsnetz gespeist wird. Der Bugatti Chiron als Spenderfahrzeug also.
Zwei bis drei Stunden parkt jeder Chiron auf dem Prüfstand, auf bis zu 200 km/h wird er im Stand beschleunigt. Das alles noch ohne Außenhülle. Die Carbon-Schale kommt erst nach Absolvierung des Prüfstandprogramms an das Auto.
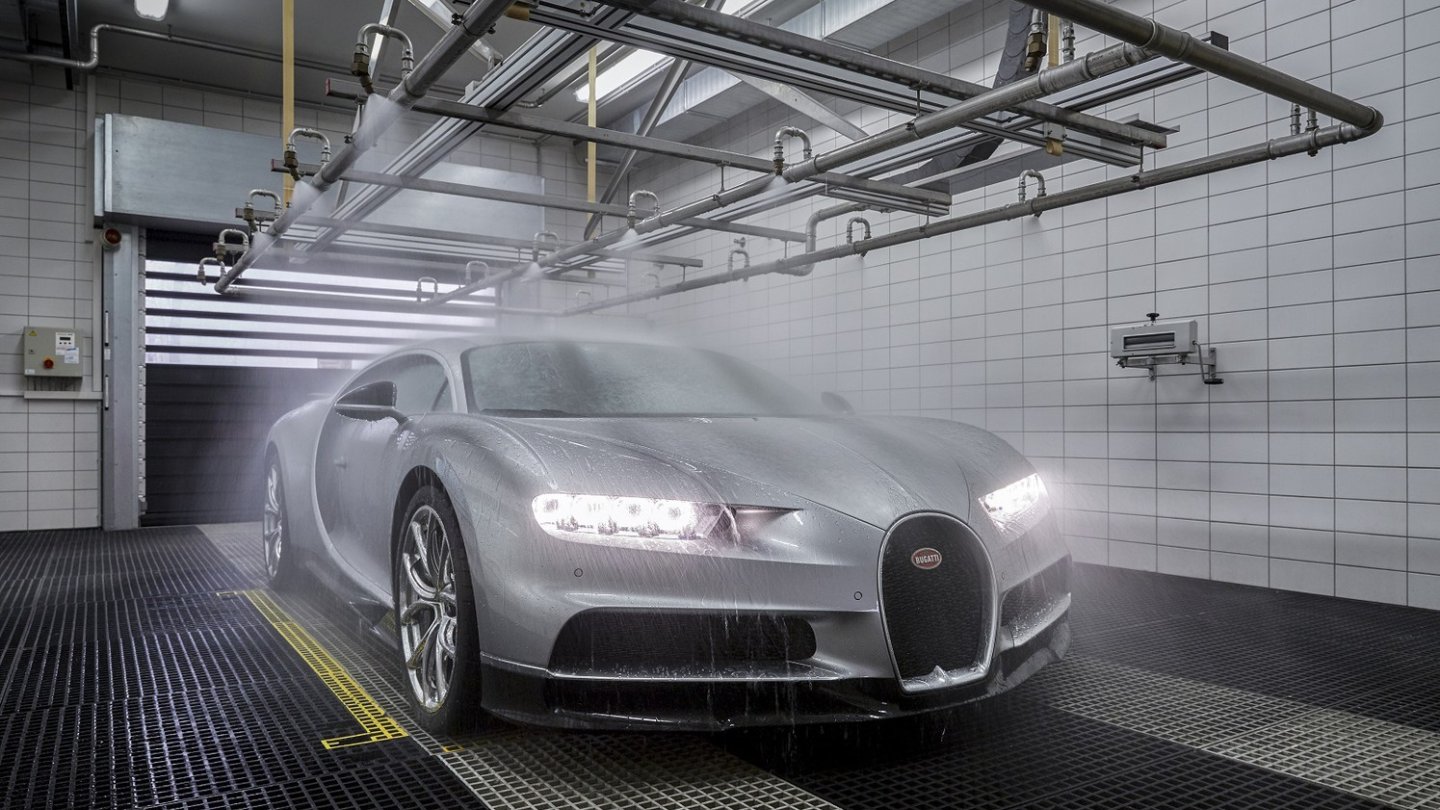
Jetzt darf er erstmal duschen, der Bugatti. Eine halbe Stunde Monsun-Regen lässt er beim Dichtigkeitstest über sich ergehen, so nass wird mancher Bugatti Zeit seines Sammlergaragen-Lebens nicht mehr werden. Ist kein Tropfen eingedrungen, wird das Interieur eingebaut. Ungefähr drei Tage dauert der Innenausbau.
Einen weiteren Tag verbringen sie bei Bugatti damit, das Auto in Kunststofffolie einzupacken. Denn jetzt beginnt der Job, für den es wohl die längste Warteschlange vor dem Personalbüro gab: Die 300 km lange Abnahmefahrt.
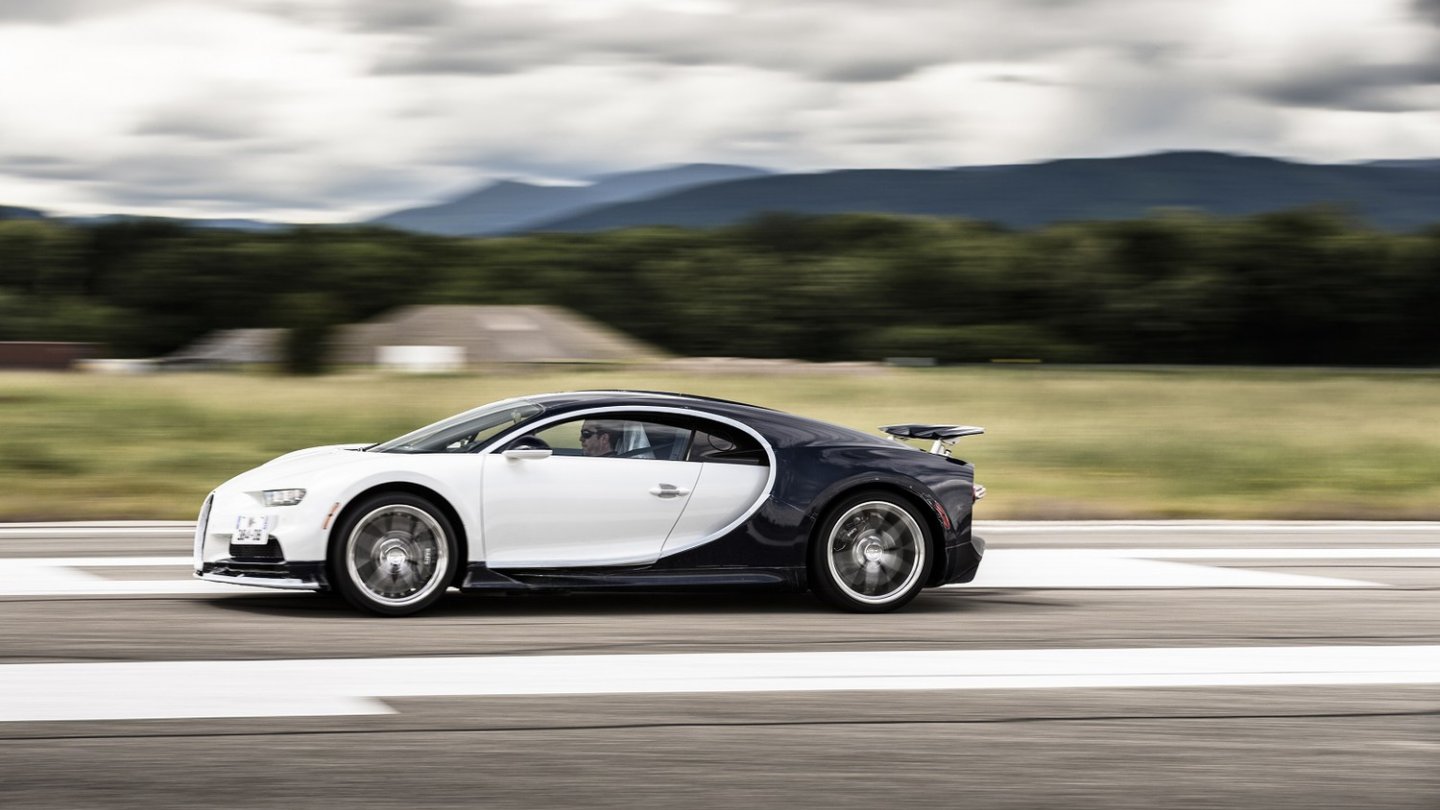
Dann erst werden die bestellten Rad-/Reifenkombination und der Unterboden ans Auto montiert, das Getriebeöl gewechselt und nach weiteren 50 km Probefahrt ein erneuter Optikcheck durchgeführt. Anschließend wird jedes einzelne Auto von Produktionschef Christophe Piochon und seinen Management-Kollegen aus Vertrieb, Qualitätssicherung und Kundendienst individuell freigegeben, bevor mit dem Kunden ein Termin zur Fahrzeugübergabe vereinbart wird.
Der laut Statistik übrigens durchschnittlich 84 (!) Autos und drei Jets benutzt. Wenn er jemanden braucht, der zum Beispiel seinen Bugatti ab und zu mal bewegt: Der Autor dieser Zeilen würde sich anbieten.